Ishida X-Ray Technology Helps to Ensure Greek Yoghurt Quality
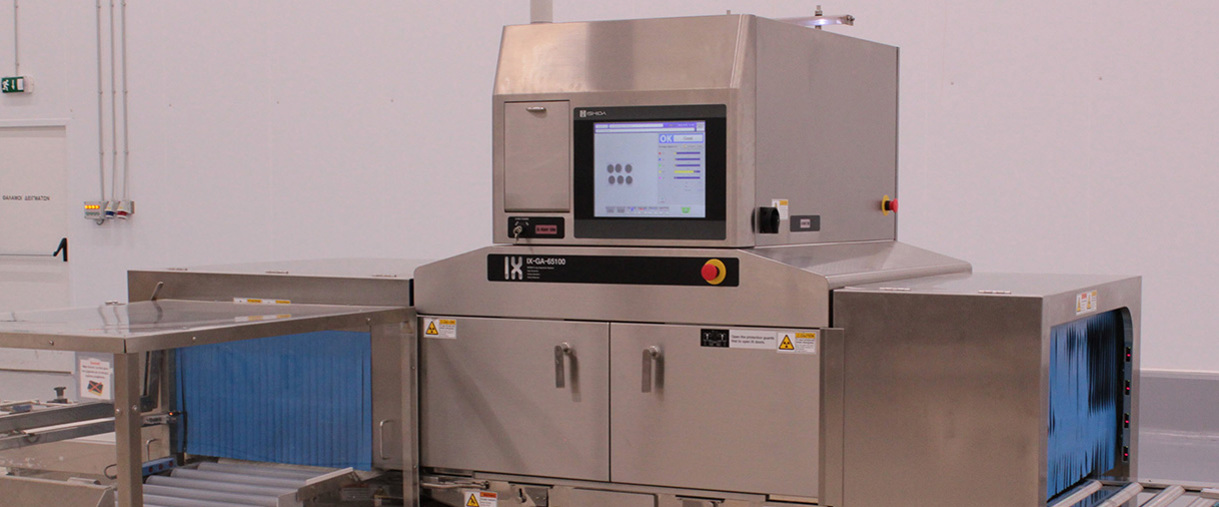

The accuracy, versatility and reliability of an Ishida IXGA-65100 X-ray inspection system is helping one of Greece’s leading yoghurt producers to deliver the highest levels of quality control and achieve continuing success in both national and international markets.
'Naturally we were looking for value-for-money from our investment but the overriding concern was quality and safety – these simply cannot be compromised, since ultimately it is our reputation that is on the line,' explains Dimitris Barboutis, Kri Kri’s Technical Manager.
Facts and Figures
Flexible
Genetic Algorithm (GA) technology, uses image data analysis over a number of inspections to achieve a an extremely high level of accuracy.
Efficient
The IX-GA-6100’s user friendly colour touchscreen enables specifications for each product to be held in the memory.
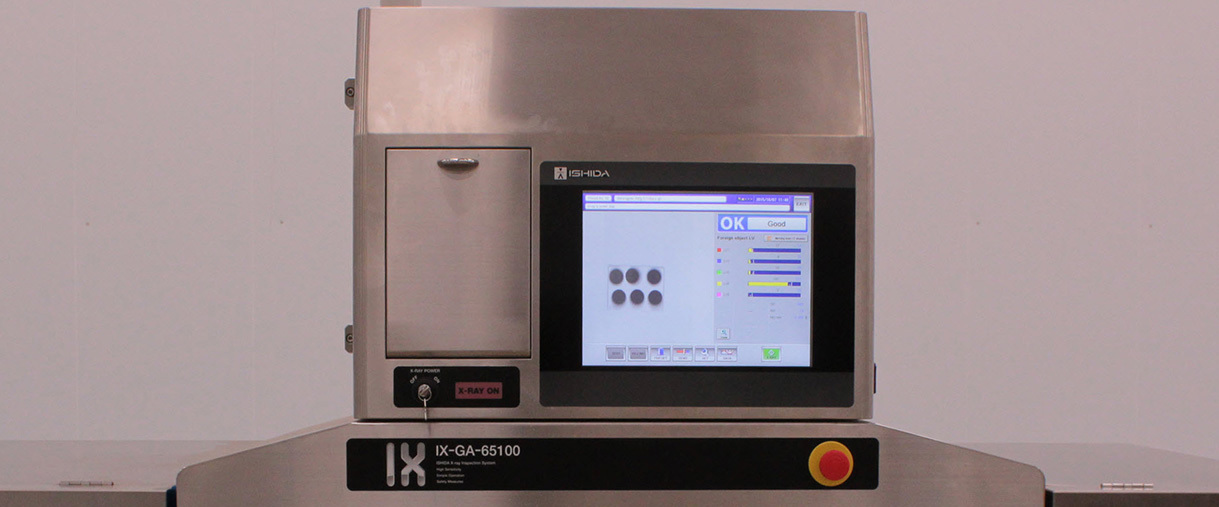
Challenge
While the advanced production processes incorporate the highest hygiene levels, it is vital that Kri Kri remains vigilant against potential foreign bodies such as metal, glass or other foreign materials that could contaminate the yoghurt if there were a problem with any of the equipment on the line.
Solution
To accommodate complete cases, the company has opted for the Ishida IXGA-65100, which is specially designed for larger products.
For Kri Kri, the major benefits of the Ishida X-ray system are its ease of use and flexibility. The IX-GA-65100’s user-friendly colour touchscreen enables specifications for each product to be held in the memory and called up at the touch of a button for fast and simple changeovers.An equally important feature of the IX-GA-65100 is its excellent versatility in its levels of detection sensitivity.
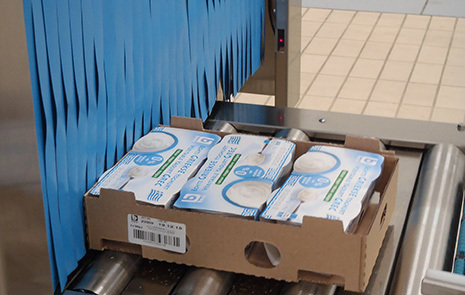
We place huge emphasis on the premium nature of our yoghurts and on our commitment to deliver the highest quality, so it is absolutely vital that we can carry out stringent monitoring to ensure that all our products leave our factory in the best possible condition.
Kri Kri’s new state-of-the-art production and packing line was borne out of an initial catastrophe when a fire on Christmas Eve 2013 caused severe damage to its dairy production plant. However, within seven months, the new facility had been created with double the production capacity. Given the opportunity to specify the newest and best equipment for the new factory, Kri Kri turned to Ishida and its Greek agent Europack for its X-ray inspection solution.
Kri Kri’s extensive portfolio of around 140 different products includes plain and fruit yoghurts, traditional varieties and a children’s range, packed in pots from 150g to 500g in size. The pots are first filled and then packed into cases before inspection in the Ishida X-ray machine.
To accommodate complete cases, the company has opted for the Ishida IX-GA-65100 which is specially designed for larger products. Like all Ishida IX-GA models, it features the company’s unique Genetic Algorithm (GA) technology, which uses image data analysis over a number of inspections to achieve an extremely high level of inspection accuracy. This enables Kri Kri to ‘train’ the machine to focus solely on the yoghurt contents in each pot, and exclude any external areas.
These numbers are well within the capabilities of the X-ray machine, but we prefer to operate it at medium to high speed in order to ensure that every pack is checked thoroughly.
Ishida X-Ray Inspection Systems for Dairy Food Producers
Ishida's X-ray inspection systems can help dairy producers detect foreign bodies such as rubber or plastic while being unaffected by foil or metallised packaging.
The machine is able to distinguish between the fruit pieces in the fruit yoghurts and any unwanted foreign bodies, and can also mask the small chocolate pieces used as a topping for children’s yoghurts which are packed in a separate plastic dome above the lid of the pot.
Kri Kri is currently processing 80-90 tonnes of yoghurt per day, with the Ishida X-ray system monitoring approximately 12,000 to 14,000 cups.
This ability to demonstrate its high quality control standards has been a fundamental part of Kri Kri’s drive into export markets, meeting growing global demand for traditional Greek yoghurt. The company’s products are now sold in 20 countries in Europe, the Balkans and the Middle East, with listings in several major supermarket chains, including the UK.
Download case study


Speak to an Ishida expert
Every business has its own challenges; ours is to help you overcome yours. Working smarter, faster, together, we can help you achieve higher standards and get your products retail ready quicker.