Nothing left to chance with Quality Control for Soto specialities
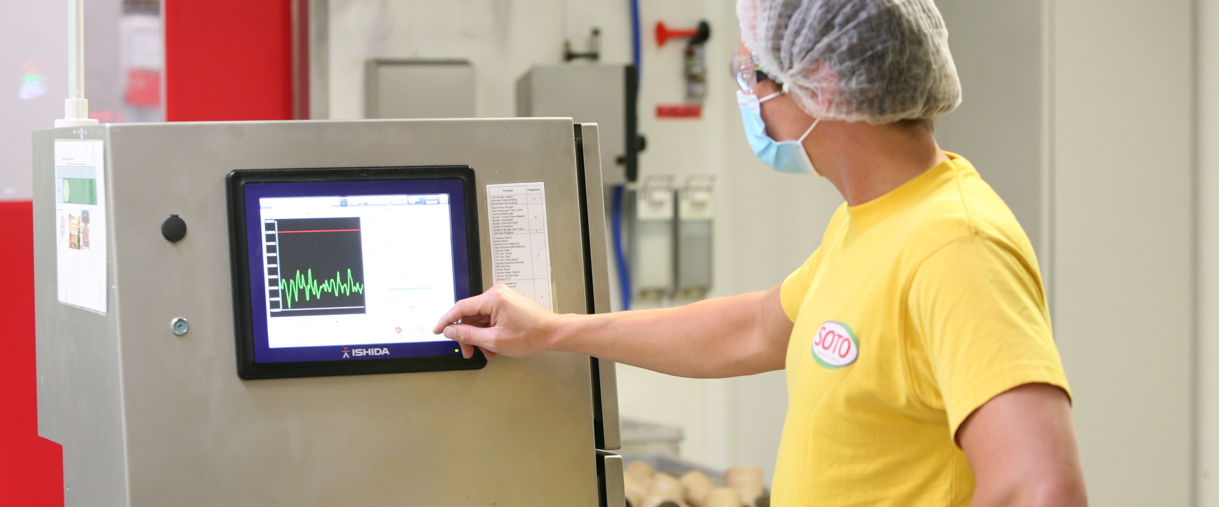
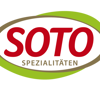
Ishida quality control and inspection solutions are helping to ensure the highest quality standards for a leading German organic vegetarian food producer. organic veggie food GmbH, based in Bad Endorf in Upper Bavaria, is using Ishida X-ray inspection, Ishida checkweighers and Ishida AirScan leak detection systems to ensure that its range of SOTO specialities - delicious ready-to-eat vegetarian and vegan organic products – reach their customers in premium condition.
Facts and Figures
Accurate
The plant-based raw materials sometimes contain natural contaminants such as very small stones or grains of sand.
Flexible
The Ishida X-ray inspection systems allow the user to select or set up particular image filtering that offers excellent detection of low density contaminants.
Efficient
The Ishida Sentinel™ online tool uses this information to anticipate machine faults or drops in performance.
Safer
For optimum shelf life all packs undergo a fully automated leak testing process before end-ofline packing.
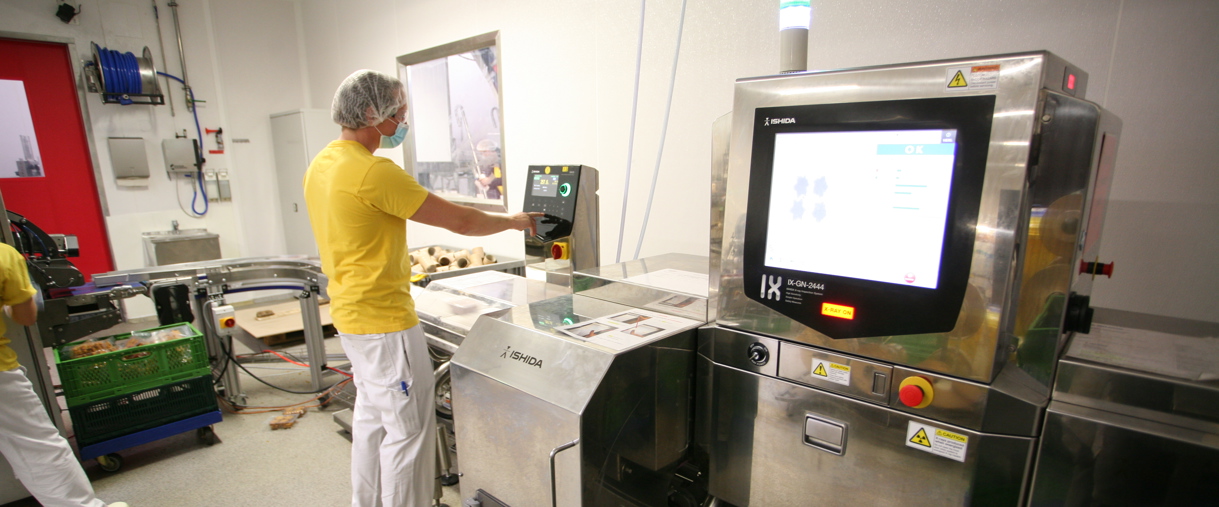
Challenge
As part of the expansion of its production, organic veggie food GmbH have built a new facility and invested in fully automated quality control systems for two of its packing lines. When organic veggie food replaced its existing metal detectors with Ishida IX-GN X-ray inspection systems, they have found the ability to detect more than metallic foreign bodies an important benefit.
“Because the raw materials in our products are all plant-based, they sometimes contain natural contaminants such as very small stones or grains of sand,” says Maria Schramm. “We can rely on the new Ishida X-ray systems to reject packed items found to contain suchcontaminants.” The systems also detect plastics and glass. “This high performance was the main factor in our decision as Ishida offered the best detection accuracy of all the candidates in our initial supplier selection process.”
Solution
Finding and rejecting contaminated products
The patented technology behind Ishida’s IX-GN X-ray inspection systems is based on software featuring an intelligent Genetic Algorithm (GA). There are seven detection levels with the first three focused on different sizes of contaminants and the last four offering GA imaging. GA imaging allows the user to select or set up particular image filtering that offers excellent detection of low density contaminants. In addition, product-in-seal software can spot any product particles in the sealing seams that could inhibit pack integrity.
Smart X-ray Inspection Systems
The Ishida IX-GN models are able to handle organic veggie food’s entire range of products in their different pack formats. Around 40 chilled and frozen products with fill weights ranging from 150g to 2.5kg are packed into bags, trays, and cardboard boxes on the two lines. There are as many as 200 pre-sets for frequent product changes, and Maria Schramm praises the X-ray inspection systems for their “extremely sensitive and accurate adjustability.”
Reliably calculating the right weight
Organic veggie food employs Ishida checkweighers on the packing lines to check compliance with statutory weight regulations. The Ishida checkweighers are exceptionally accurate with its large weighing range, that offers tremendous flexibility. The operator can switch between two weight range settings with different graduations at the touch of a button. This means that the checkweigher can be used for a wider range of products. Should excessive force be unexpectedly applied, the patented Force Dislocating Limiter (FDL) automatically disconnects the weigh sensor from the weighing conveyor. Once rectified, the checkweigher can immediately resume operation.
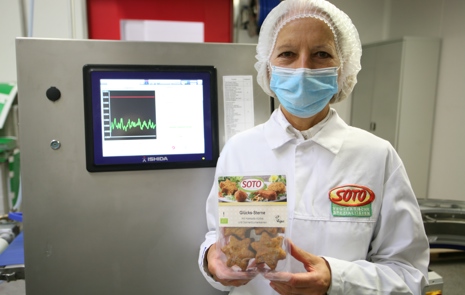
Ishida offered the best detection accuracy of all the candidates in our initial supplier selection process.
In-line leak detection for all packaging
SOTO specialities are free of preservatives, and an intact protective atmosphere is essential to guarantee the products’ shelf life. For this reason, they undergo a fully automated leak testing process before end-of-line packing. The Ishida AirScan systems use laser technology to detect leaks of carbon dioxide (CO2) from the modified atmosphere of the packaging. The high-performance systems inspect every single pack from all sides in less than 20 milliseconds. They are able to find leaks in the sealing seams and holes as small as 0.25 mm at speeds of up to 180 packs per minute, while the completely non-destructive inspection process cuts material costs as well.
The Ishida AirScan systems are very easy to operate and require almost no maintenance. No adjustments to settings are needed for product changeovers; only the height-adjustable control arm with the sensor head has to be altered to the different pack heights. “The leak detection process with the Ishida AirScan systems has definitely taken our internal quality assurance procedure to a whole new level,” confirms Maria Schramm.
The leak detection process with the Ishida AirScan systems has definitely taken our internal quality assurance procedure to a whole new level.
Online software keeps a close eye on production
organic veggie food is also now employing its new quality control systems to further optimise the packing processes for its SOTO specialities.
The Ishida Sentinel™ online tool uses this information to anticipate machine faults or drops in performance. Trends, batch information and statistics can be visualised on a case-by-case basis and sent out as reports.
“Our company’s recipe for success is that we are flexible, fast, inquisitive and open-minded,” concludes Maria Schramm. “We apply that approach to the technology we use as well.” Indeed, the company has already ordered another X-ray inspection system from Ishida.
Download infographic


Speak to an Ishida expert
Every business has its own challenges; ours is to help you overcome yours. Working smarter, faster, together, we can help you achieve higher standards and get your products retail ready quicker.